Technology is what pushes every business forward regardless of industry. Delivery companies are no exception, as innovations have made the industry more efficient and competitive. With the dominance of e-commerce and last mile delivery design, businesses will now have to find ways to move goods to customers even faster. Thus, logistics and parcel companies must find ways to improve their operations, or else they'll end up eating dust their competitor's dust.
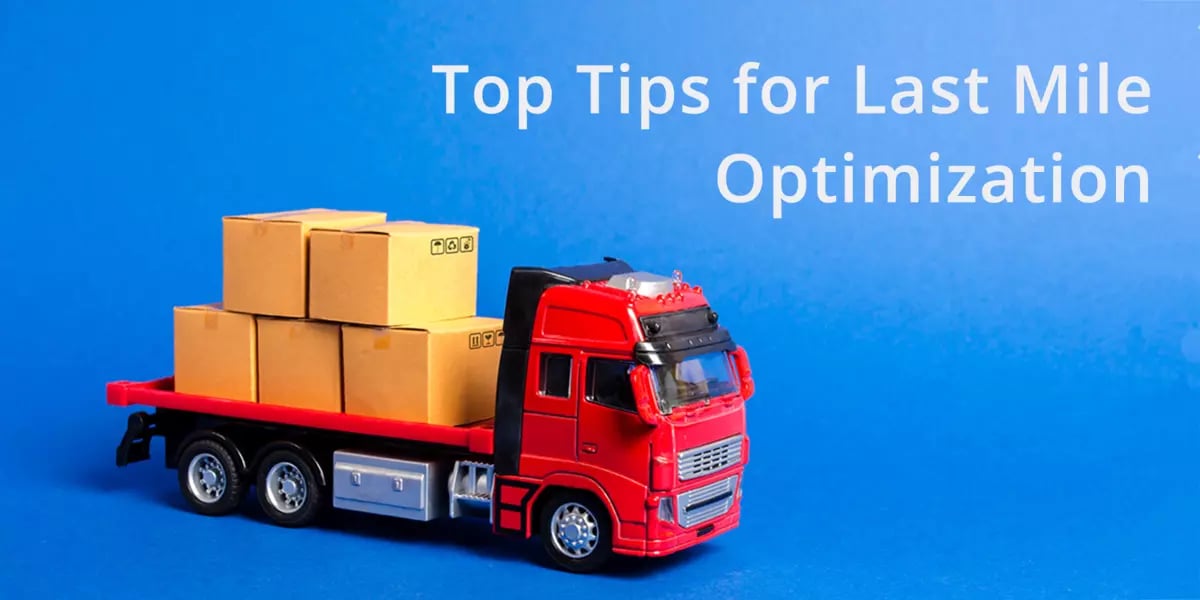
Why is Last Mile Delivery Optimization Important?
Within the hierarchy of the supply chain, last mile delivery is the most time-consuming and expensive step of the delivery process. Delivering ordered items to each customers' doorstep means dealing with heavy traffic for urban areas or having miles between delivery points for rural locations. So it's easy to see that inefficient supply chain practices on the last mile can reduce profits significantly. Thus, companies need to think hard about last mile delivery optimization when it comes to their logistics planning.
Businesses must now start evaluating their processes to determine where the biggest inefficiencies lie and how to address them best. Finding these improvable connections in the chain is essential for a valid last mile delivery plan so businesses can boost their revenues.
What Are The Steps In Creating An Effective Last Mile Design?
The universal process for last mile delivery design is composed of six steps:
Creation of a Centralized System
Like with most processes, the first step is the most crucial in last mile delivery planning. Arguably, delivery companies vary on how they process and store data on orders and stops into their system. What's important is having a centralized system where everything that's placed in a vehicle is marked, listed, and tracked properly.
Ensuring Last Mile Delivery Route Optimization
One of the best ways to optimize profits for delivery companies is to optimize their routes. This is true for all firms regardless of their delivery capacities. Optimizing all route planning is the only option, especially for those handling hundreds or thousands of deliveries a month.
Fleet managers should input tasks and assign them to drivers at the start of the day so drivers can plan out their activities precisely for the entire shift.
Organized Sorting of Packages
Proper segregation of parcels is crucial for any company so they can be loaded onto the trucks in an orderly, yet quick fashion. Logistics firms that work with local partners must segregate which goods are to be delivered by their in-house team and those that will be handled by a third-party entity. Proper organization and sorting out of parcels entail special software and expendable materials like barcodes to be affixed to merchandise.
Scanning of All Goods Before Loading
Automation of the entire supply has its advantages as it provides greater visibility of all the goods for delivery and their movements while inside vehicles. Thus, it is imperative to scan all items to be delivered before they are loaded in the trucks. Scanning is easy, and can now be done with most mobile phones or devices loaded with the proper apps, provided there are bar codes ready or in place. The centralized system can then track the whereabouts of any particular good in real-time.
Engaging Customers in the Delivery Process
Technology has changed consumer behavior significantly as most buyers want to track their orders from the moment they make a purchase. A great supply chain these days involves the customers in the process with more transparency than has ever been available before. For businesses, this means providing a map showing the customer the location of the driver in real-time, live tracking, and a constantly updated ETA. Aside from the ability to track their orders, consumers want the ability to communicate directly with the drivers. Allowing a free flow of communication between them and the driver will improve customer confidence and significantly reduce missed deliveries as well.
Centralized Storage of Verifiable Delivery Records
The high volume and quick pace of deliveries can cause drivers and their organizations to lose hard copies of the proof of delivery. Fortunately, automation produces digital records—aka a paperless workflow— that are sent and stored at the central system. The centralized records of all digital, proof of delivery, make handling of customer complaints and disputes much more manageable.
Businesses engaged in last mile deliveries must ensure optimal operations and proper organization in every step of the supply chain process. Fortunately, technology allows for automation and centralization of data, which in turn helps in the creation of cost-effective and efficient delivery operations for the long haul.