Delivering to end-users is a complex, time-consuming, and expensive process no matter what business you’re in—but the last mile is particularly challenging for food wholesalers. Quality assurance, expiration dates, and regulatory policies are difficult to handle on top of the usual final mile problems.
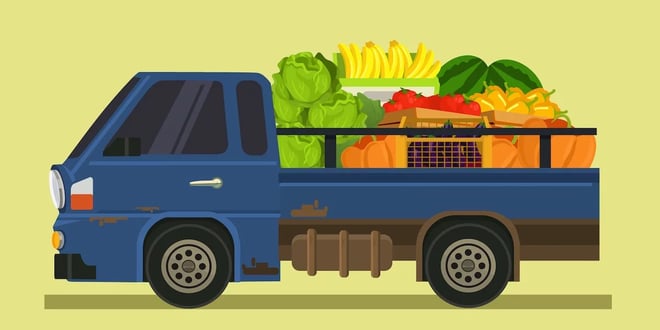
Food wholesalers aren't only dealing with irate end-customers when they experience delivery delays: For one thing, food quality can impact people’s health, which puts added pressure on drivers and dispatchers to successfully track operations in real time. For another, you’re more likely to be dealing with B2B delivery scenarios, in which one delivery snafu could jeopardize a longstanding relationship. On top of all this, you need to find a way to keep operating costs from spiraling out of control.
Major Last Mile Challenges for Food Wholesalers
Food and beverage logistics operators are facing last mile challenges that others don’t. For instance:
Timely Loading and Shipping of Produce
Ideally, businesses must load the produce as soon as they have been selected and packed. Shippers must be attentive to the fact that some food items, such as fruits, should not be transported in the same trucks as fruits that release ethylene. Ethylene can cause specific fruits like peppers and tomatoes to ripen and spoil faster—matching the right orders to the right trucks and drivers is always a challenge, and this simply adds to the complexity.
Proper Food Handling
The food industry losses billions of dollars every year due to spoiled food during transportation. Studies show that around a third of food in the US is wasted or lost, and that fresh produce spends 50 percent of its shelf life in the shipping process. Food losses are normally caused by the spoilage of food during the transportation stage, and the damage sustained by vegetables and fruits that prevent them from getting bought.
Below are some of the reasons for food losses due to improper handling during shipping.
Impact damages
Consumers normally avoid buying damaged or bruised produce. Those that end up damaged during transportation won't make it to grocery shelves or stores.
Temperature and humidity
Shippers must ensure that both humidity and temperature are controlled and maintained at the right levels so produce is kept safe and fresh during their transportation. Keeping produce refrigerated in last mile trucks is necessary as rising temperatures can cause bacteria to grow.
Of course, the requirements for keeping food safe and fresh differ from one product to another, which adds an extra wrinkle for wholesalers.
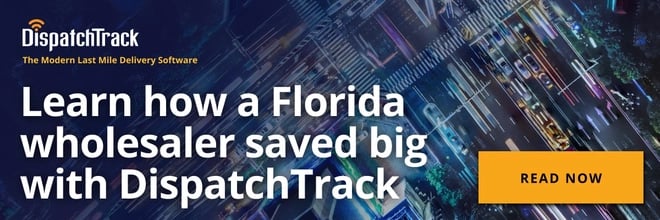
Product Quality and Safety
Product recalls can disrupt food distribution significantly. And in recent years, supply chain networks have become more diverse, exposing consumers to a wide range of food products. This diversity, however, also increases the risk of safety failures. The Food and Drug Administration (FDA) is cracking down on food product safety failures, with the agency issuing warning letters to many food companies in recent years.
Wholesale food sellers face multiple business risks if they fail to secure the safety of their produce. Food companies must be able to go through their entire chain as quickly as possible when recalls are made. Businesses should be able to pinpoint quickly if they have received a specific product and the exact location of the food product being recalled.
Supply Chain Disruptions
Time is of the essence when it comes to transporting food products. Other industries such as retail will receive backlash from their consumers when the deliveries are delayed. But in the food business, delays can mean huge profit losses due to food spoilage.
Unfortunately, supply chain disruptions of various sorts can make life difficult. Weather disturbances, for example, can prevent food producers and shippers alike from transporting produce from one place to another. Likewise, major disruptions such as the lockdowns brought by the COVID-19 pandemic disrupt everyone's supply chain, including those of the food industry.
How Technology Can Impact Last Mile Optimization in Food Logistics
To optimize their last mile operations, food wholesalers must invest in technological solutions. Here's how technologies can help food enterprises overcome last mile challenges:
Create real-time communication channels
Time is important in food logistics. Any delays, such as drivers waiting for loading of produce into trucks or delivery trucks stuck in traffic, can cause more food loss. Having communication channels that allow for transparent and real-time communication will help solve problems since every team across the supply chain is well informed of current issues. Real-time communication helps management and employees solve problems quickly. Again, this can be particularly impactful in B2B situations where customer communication and relationship-building is paramount.
Automate processes
It's the digital age—but many businesses still rely on Excel sheets, pen and paper logging, and manual route planning and dispatching. Eliminating inefficiency requires ditching manual processes in favor of automated solutions.
Take route planning for example. Planners spend many hours planning routes and yet they can't account for all the variables needed to come up with the most optimal routes. Automated route planning, on the other hand, takes into consideration all elements affecting delivery times, and can provide dispatchers and drivers with the best routes to lessen the travel time and avoid food spoilage and keep to agreed-upon delivery windows. In other words, it helps ensure that your trucks don’t show up in someone’s parking lot in the middle of the lunch rush.
Boost visibility throughout the supply chain
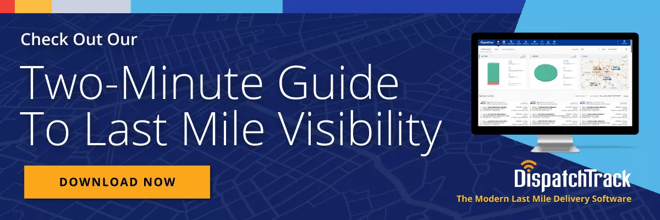
Technological solutions like a delivery logistics platform that addresses visibility problems are beneficial for food producers and shippers. They allow food distributors to view the big picture by getting accurate information immediately from all stakeholders. Having visibility means having the ability to trace the products or inventory in real-time. In case of recalls, businesses can then trace the product's actual location or where it was delivered—the rest of the time, it means easier exception management on the day of delivery.
Final mile operations involving whole food will always be filled with complexities and challenges. But food enterprises can still optimize their last mile processes with careful planning, automation, and the right technological tools.