Logistics play a vital role in the global economy. Globalization has pushed many companies to outsource logistics operations to third-party logistics providers (better known as 3PLs), to focus on their core competencies. But logistics operations are incredibly complex, which is why 3PL companies are facing more challenges than ever in the global supply chain.
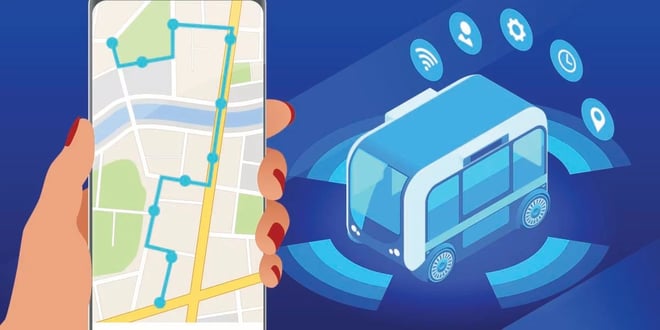
Understanding 3PLs
Now more than ever, there are any number of reasons e-commerce firms or retailers are outsourcing their needs to 3PLs.
High Order Volumes
E-commerce is growing rapidly, and many businesses are struggling to meet the higher volume orders. Those who can no longer keep up with higher demand outsource some of their functions rather than risk losing their customers to competitors.
Lack of Inventory Space
Many businesses are running out of storage space for their inventories. Some companies choose to engage with a 3PL warehouse to meet the higher order volumes and manage their inventories more effectively. Outsourcing to 3PLs allows businesses to grow their product lines without renting or purchasing additional space for storage.
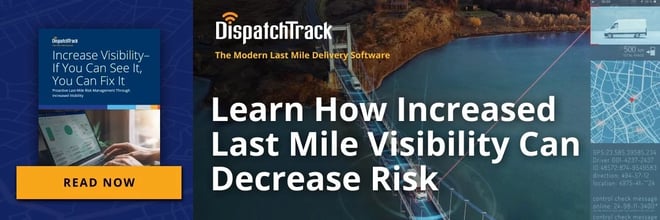
Offering Additional Delivery Options
Last mile delivery plays a crucial role in meeting consumers' expectations. These days, retailers must provide excellent delivery services as the last mile is now a top brand differentiator, displacing product and pricing. Businesses must provide more delivery options and better service than ever before. Outsourcing to 3PLs is an alternative to managing in-house fleets or adding more vehicles and drivers to augment current fleet capacity.
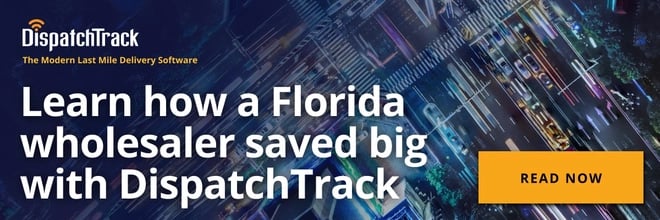
Top Challenges for 3PL Firms
Fluctuating fuel prices, lack of talent, poor collaboration, and changing regulations are just some of the challenges 3PL companies must overcome in order to thrive in the modern economy:
Rising Fuel Costs
All businesses with delivery operations are dealing with rising fuel costs. After all, fuel expenses account for a large chunk of many businesses' operating costs, and high fuel expenses can cut into a company's revenue quickly.
Recruiting New Talent
One of the pressing problems the delivery industry is facing is the difficulty of attracting new talent. Many firms are complaining that it’s too challenging to find the right employees for their vacancies, with many candidates lacking the skill or experience to match the job requirements.
It doesn't help that the transportation industry has been dealing with a driver shortage for years. Annually, the American Transportation Research Institute (ATRI) surveys industry players for their most pressing issues, and driver shortage has been named in the industry's top five concerns for the past several years.
The lack of qualified talent results in loss of productivity and efficiency, which is problematic for 3PL firms whose margins can’t usually stand up to decreases in efficiency.
Lack of Collaboration
Carriers and transport providers' role in supply chain operations can never be stressed enough. But too often, their importance is overlooked at an operational level. The lack of cooperation—to say nothing of communication or supply chain integration—among carriers, shippers, and customers adversely affects the supply chain's smooth operation.
Government Regulations
Most 3PL firms transport goods in different cities, states, and even countries. As such, they must adhere to the rules and regulations of these different areas. Government regulations vary from one locality or state to another, and 3PL companies must be updated and compliant with all these rules to continue operating smoothly. This is a challenging task, as many 3PLs don't even have access to appropriate human resources who can handle and keep track of the changing and varying regulations.
Environmental Concerns
There's a growing concern about the impact of transportation on the environment. Emission reduction and anti-idling regulations imposed by local and state governments are worrying industry players. Compliance with these regulations can cost businesses money if they don’t find a cost-efficient way to cooperate with them.
Client Requirements
Clients’ requirements vary considerably from business to business, and meeting each client's needs is a challenge facing many 3PL firms. Increasing customer demands for fast shipping and real-time visibility on delivery status are becoming major sources of headaches for 3PLs who haven’t kept up to date when it comes to technology.
Absence of Reliable Reporting Mechanisms
Even mid-sized 3PLs can have a hard time keeping track of all the shipments being sent out. Asking vendors about shipments done to generate a monthly statement is no easy task. The absence of a reliable reporting system can stick 3PLs with high labor costs and even revenue losses as manually tracked inventories and shipments are prone to human error.
How Technology Helps
Technological solutions play a vital role in addressing the many challenges facing 3PLs today. Delivering services to clients satisfactorily requires investing wisely in technology. 3rd party logistics software solutions that can help deliver to end customers optimally (whether those are other businesses or B2C consignees), integrate with clients’ systems, enable real-time communication, and provide end-to-end proof of delivery will greatly help 3PL companies.
Here's how technology helps 3PLs:
Real-time visibility
Companies can improve all aspects of their operation by investing in real-time visibility. When you can see what’s happening across the entire last mile, you can more easily manage by exception—taking proactive steps to reroute missed shipments, avoid traffic jams, or reschedule shipments based on changing customer needs.
Improved Collaboration
Automating the supply chain systems and processes go a long way in enhancing collaboration between 3PLs and their clients. An integration of systems paves the way for quicker supplier onboarding and optimization of last mile deliveries.
Better collaboration also helps manage unexpected events such as natural disasters or inclement weather, as all stakeholders can communicate with each other in real-time.
Deeper Insights
Automating the supply chain will provide better data on operations, which executives can use to identify pain points in their operational processes. With solutions that offer customizable reports, you can drill down on the exact KPIs that you want to focus on and then work to improve them over time. Like we saw with real-time visibility above, it’s much easier to be proactive if you have all the facts at your disposal.
3PLs face many pressures these days, but fortunately for them, these challenges can be overcome by using modern technology. Advanced 3PL management software solutions help reduce wasted time, lower operating costs, and optimize their every day processes.